In Florida, opened a new technology for 3D printing of houses
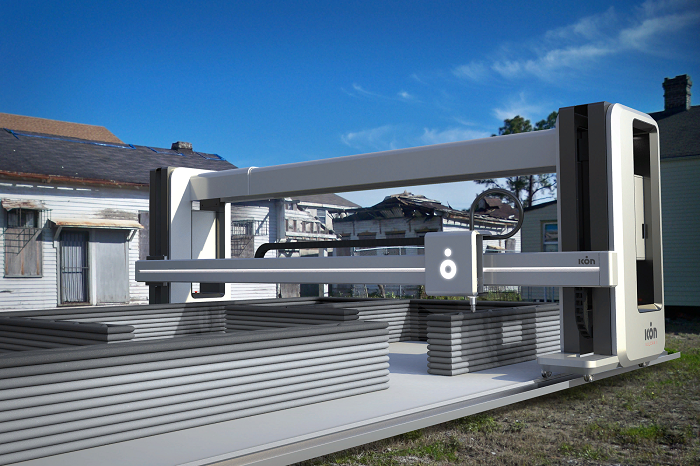
While the federal government and the Federal Reserve have set themselves the task of paying off debt by raising asset prices with huge cash injections, the problem of buying a home has become very urgent for millions of ordinary Americans.
To counter skyrocketing prices for everything from lumber to concrete, builders have turned to 3D printing technology.
Last week, construction began on the first 3D-printed house in Florida in Tallahassee.
“I need to pinch myself,” said Kindra Light, co-owner of the firm behind the Precision Building and Renovating project. “I can’t believe this is really happening.”
Kindra and her husband James Light have taken up 3D printing to provide affordable housing for all Florida residents.
Construction began last Thursday on a piece of land in northwest Tallahassee and should be completed by the end of the week. The automated printer is suspended from four poles and stacks about 60 cu. see concrete per day.
Printing walls out of concrete is instead of building houses out of lumber. Thus, you can save money, reduce labor costs. All you need is a small team and a printer that.
Building a house with three bedrooms and two bathrooms takes eight to ten weeks. It will cost about $175,000 to $200,000, Light said. The savings are significant given the average rise in US residential property prices to a record $350,000 last month.
“This is the future,” said Chase Miller, founder of construction company Urban Land Co., who traveled from Ohio to look at the house’s print. “This technology has so many possibilities and it can really help people.”
Miller said it could be a great tool for rebuilding homes after hurricanes because the printer is fast.
About a month ago, a house in South Richmond, Virginia, became the first 3D printed home under construction in the state. The builders wanted to save on costs and make the house affordable, given that lumber prices have soared over the past year.